6 erros comuns em Inspeções de Qualidade a serem evitados
22 janeiro, 2018
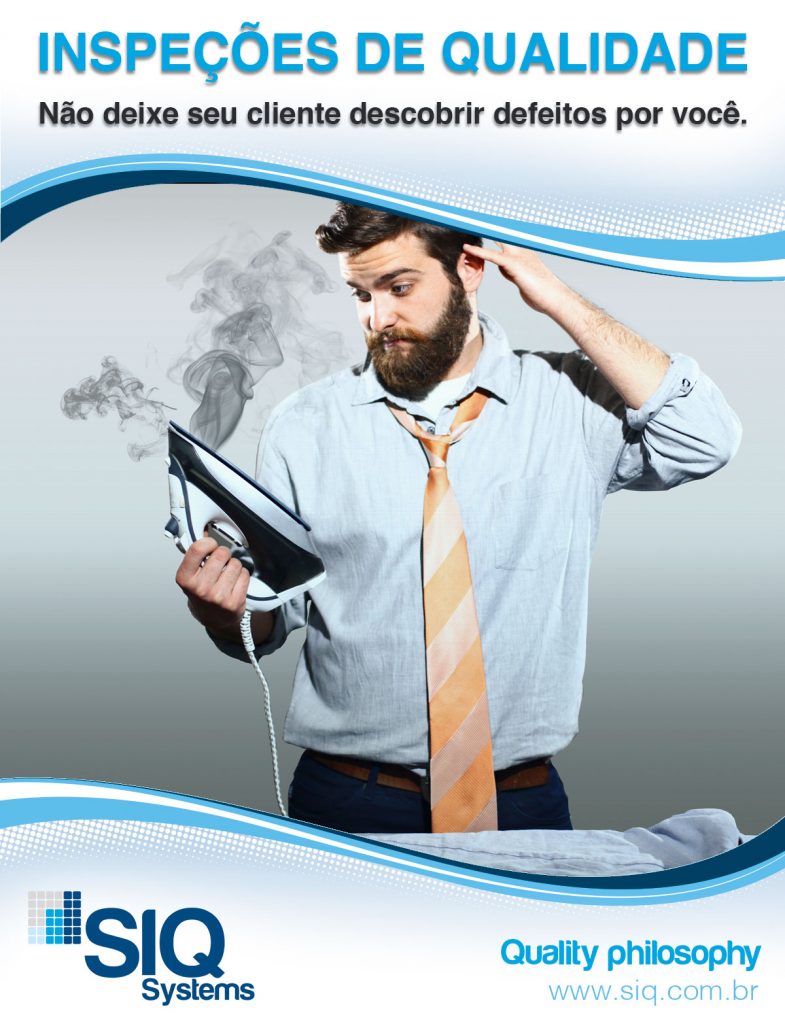
6 erros comuns em Inspeções de Qualidade a serem evitados
As inspeções de qualidade são vitais para identificar e corrigir problemas em produtos e processos produtivos, evitando defeitos e recalls antes de chegarem no consumidor final. Ao mesmo tempo, a alta competitividade entre as empresas gera grandes disputas pela liderança de mercado, aumentando ainda mais a importância de entregar produtos com alto nível de qualidade.
Usando como base nossa experiência em desenvolver soluções para todos os pontos de controle de qualidade presentes em uma empresa, elaboramos uma lista com 6 erros comuns cometidos pelas organizações quando se trata de Inspeções de Qualidade. Confira:
1. Não conhecer com profundidade os requisitos do mercado
Ter conhecimento aprofundado acerca das regras, legislações, normas e requisitos obrigatórios dos produtos do segmento em que uma empresa atua nem sempre é fácil. Porém, é fundamental garantir que todas essas exigências sejam atendidas, assegurando o comprometimento que a empresa tem em garantir a qualidade e segurança dos produtos fornecidos.
2. Falta de treinamento e padronização
A qualidade de um produto ou serviço é o resultado de um esforço conjunto de muitos colaboradores, muitas vezes contando com materiais fornecidos ou serviços prestados por terceiros. A preservação da qualidade depende de que este esforço seja um compromisso diário feito com excelência e atenção aos detalhes.
Oferecer cursos e treinamentos e manter sempre viva a padronização dos processos servirá para que os colaboradores possam compartilhar um propósito comum em prol da qualidade. É através de cursos e treinamentos que os funcionários aprenderão como realizar suas atividades, disseminando conhecimento e informação para que os processos funcionem atendendo aos requisitos necessários possibilitando a melhoria contínua.
3. Realizar o controle de dados em planilhas
Embora amplamente utilizadas por empresas, sendo uma excelente ferramenta para compilação e análise de dados a curto prazo, as planilhas não são ideais quando queremos gerenciar uma grande base de dados continuamente – principalmente quando muitas pessoas precisam ter acesso às mesmas informações de forma simultânea.
O melhor cenário para que uma equipe possa focar no seu core business é implementar um sistema de gestão empresarial abrangente, com interface ERP, alta performance de navegação e que permita compartilhar informações em tempo real por todos os envolvidos.
Existem outros pontos nos quais as planilhas não são boas o suficiente quando se trata de gerenciamento da qualidade, entre eles:
- Vulnerabilidade a fraudes – qualquer pessoa que tenha acesso a planilha ou rede em que essa planilha se encontra pode alterar fórmulas, valores e dados facilmente;
- Baixa confiabilidade – planilhas são mais suscetíveis a erros de digitação, e por mais que esses erros pareçam inofensivos, podem abalar a credibilidade das informações e levar os gestores a tomar decisões ruins. Além disso, basta uma distração na hora de salvar os dados e as informações podem ser perdidas para a sempre;
- Não geram indicadores automaticamente – as planilhas não foram feitas para armazenar dados históricos, sendo assim, torna-se muito trabalhoso transformar dados em informações úteis para análises gerenciais do dia a dia bem como obter histórico de lições aprendidas;
- Lentidão – principalmente quando essas planilhas possuem uma grande quantidade de dados.
4. Basear-se única e exclusivamente no Certificado de Qualidade emitido pelo fornecedor
Exigir de fornecedores Certificados de Qualidade é uma prática muito comum entre as empresas. Embora esses certificados sejam valiosíssimos para comprovar que o produto foi montado conforme especificações e exigências legais do cliente, eles não garantem por completo a conformidade do produto fornecido.
Além de exigir Certificados de Qualidade aos seus fornecedores, o ideal é que as empresas realizem inspeções dos lotes recebidos utilizando-se critérios de importância pré-estabelecidos. Dessa forma, as empresas evitam que defeitos sejam descobertos tardiamente – na inspeção final ou, em casos piores, pelo próprio cliente, causando muitas vezes danos irreparáveis para a credibilidade da empresa no mercado.
Outra possibilidade é a realização de Inspeção na Origem, ou seja, antes que o produto seja enviado para o cliente. Com isso, sua empresa garante que os produtos entregues pelos seus respectivos fornecedores cheguem com qualidade assegurada, eliminando custos e desperdícios advindos de produtos defeituosos.
5. Não ter um Planejamento para Controle
O Planejamento de Controle tem como principal objetivo reunir características críticas de um produto ou processo que necessitam ser monitoradas e controladas durantes as inspeções. Assim, é possível detectar de forma antecipada e preventiva possíveis falhas nos itens em análise, com a vantagem de compartilhar informações importantes para os colaboradores envolvidos no processo em tempo real.
Ao realizar inspeção tendo como base um bom Planejamento de Controle, a empresa garante que as etapas sejam previamente verificadas, permitindo que as irregularidades e não cumprimento dos padrões estabelecidos sejam identificados precocemente. Isso gera maior agilidade para o processo, aumento da qualidade do produto, e, por consequência, a satisfação dos clientes.
6. Utilizar equipamentos de medição não calibrados
Monitorar o desempenho de um equipamento de medição com periodicidade é vital para garantir a qualidade dos produtos e processos. Pode parecer algo óbvio, mas muitas empresas não se atentam como deveriam para essas atividades.
A utilização de equipamentos em condições anormais, ou seja, aqueles que estão fora dos padrões de qualidade propostos pelas normas dos órgãos competentes, comprometem negativamente a qualidade dos processos onde esses equipamentos são utilizados, gerando produtos defeituosos e de baixa qualidade.