Distribution Center Quality Management
Reduce the problems of quality in the Distribution Center, causing the reduction of breaks, ruptures and logistics costs, allowing it to identify the root causes.
SIQ Distribution Center Quality Management Suite is composed of the following modules:
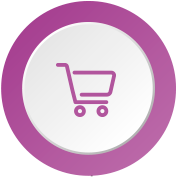
Distribution Center Quality Management
-
Documents
This allows you to comply with regulations, procedures, designs and work, preventive maintenance, and safety instructions, among others, locally or corporatively within the company – DCs and stores.
-
Assessment/ Audits
- It allows you to implement and manage internal audits in DC and store processes.
- It controls results and next audits.
- Action follow-up.
- Example of audits: Productive Process / Quality System / Sanity.
-
Plataform Inspection
It allows you to control the products while they are in the DC and when they leave the DC through sampling tables (parameterizable), skip lot and technical files, automatically generating performance indicators and nonconformity notifications internally.
-
Non Conformities
It allows you to create, manage and provide action needs whenever nonconformities occur, providing root-cause analysis and troubleshooting through tools such as 8D and 5PB’s.
It can also be used as a repository of continuous improvement actions, allowing you to create and monitor action plans and their results (PDCA, DMAIC etc.). -
Packaging Conformity
It allows you to control the products while they are in the DC and when they leave the DC through sampling tables (parameterizable), skip lot and technical files, automatically generating performance indicators and nonconformity notifications internally.