New Product Development Management
The New Products Development is a strategic factor of extreme importance so that companies in the automotive sector can maintain their competitiveness and expand their participation in this market in constant evolution.
SIQ Systems New Product Development Management Suite is a powerful management tool that automates the management of New Product Development and its changes, ensuring process standardization and shared information management with the involved areas and their respective suppliers, supporting the Implementation and product management decisions, reducing risk and maximizing market opportunities.
This tool allows full control over the project schedule, automatically informing those responsible to execute their activities within the established deadline, and allows the updating of all documents changed due to changes in an agile and comprehensive manner.
SIQ New Product Development Management Suite is composed of the following modules:
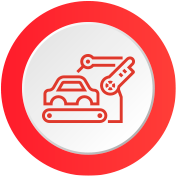
New Product Development Management
-
Process Flow
The Process Flow gathers all stages of a given process through a clear symbology, with the aim of showing, in an uncomplicated way, all flow of information that aim to improve the understanding of the processes, as well as the creation of standard norms of work to Be followed. The Process Flow has a list of phases dependent on each other, and each phase has one or more related FMEA Standard. In addition, because the Process Flow is versionable, it is possible to insert attachments when there is a need to insert engineering revisions, changes in job descriptions, responsibilities and authorities, for example.
-
Process FMEA
The purpose of the Process FMEA is to analyze the possible flaws in the planning and execution of a process, in order to minimize and eliminate the occurrence of faults and to define corrective actions on the faults found. The Process FMEA has numerous advantages for the company and its respective customers. For the company, the Process FMEA provides the cost reduction, coming from an effective procedure with less chances of failure and waste. In the case of the customer, it is spared from purchasing parts with manufacturing problems that put its safety at risk, avoiding its dissatisfaction, which, again, is beneficial to the company’s image again.
-
Product FMEA
DFMEA implements FMEA in the project scope. It predicts potential failures in product creation and allows you to define actions for causes in order to reduce Severity, Occurrence, and Detection indicators.
-
Standard FMEA
FMEA Standard Function is a central module of functions that will be used in other modules. It allows functions to be reused in different FMEAs, reducing the time of registration and analysis and providing fast changes in complex structures.
-
APQP/PAPP
The Approval Process (APQP) combines all documents related to a product structure (BOM, in “quality vision”). It offers a requirement tree containing all items in this product structure, as well as the result of all its document workflows.
-
Engineering Change
In the Engineering Change module, engineering modifications are established for fault correction that adversely affect the shape and functionality of the product. This module is intended to correct design errors and to provide improvements in the manufacture and assembly of parts, ensuring that everything is done in the latest version of the design.
-
Q.I (Quality Instructions)
Organizes the guidelines for the control of the records that make up the Quality Management System (QMS). It covers all the identification, collection, indexing, access, archives, storage, maintenance and disposal of technical and quality records.
-
Control plan
The Control Plan gathers critical characteristics about a product or process, in order to provide means to detect possible flaws in the item under analysis. After approval of the Process FMEA Workflow, the Control Plan can be prepared manually or automatically generated by the system. The rejection of a Control Plan reopens the Process FMEA, causing the Control Plan to be reopened after the new approval of the Process FMEA.
-
BOM – Bill of Material
The purpose of the BOM (Product Structure) module is to provide a detailed record with information on all components, raw materials and items used to obtain a product, identifying all the precedence and correct quantity relationships for each item required. This module can integrate with the customer’s ERP.